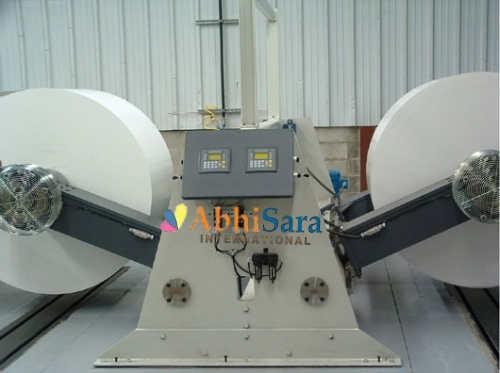
The system includes a tension controller, an air filter, an electronic-pneumatic converter, a sensor collar, and a proximity sensor.
The sensor mounts on the roll stand’s arm and monitors the number of rotations, detecting the proximity of the sensor collar.
This signal is fed to the tension controller, which reduces the diameter. For the maximum roll diameter, the controller sends the maximum voltage to the electro-pneumatic (E-P) converter.
As the roll diameter reduces, the voltage lessens proportionately. The EP converter translates the voltage to air pressure. As the voltage decreases, the air pressure fed to the roll stand brakes is reduced.
Features
- “Proportional Type” design
- Load cell or dancer roll mechanisms unnecessary
- “Low Roll Diameter” detection
Benefits of Using Automatic Tension Control
- Automatically reduces brake pressure as roll diameter decreases
- Simplifies threading procedure while maintaining consistent tension
- Automatically stops sheeter when a minimum diameter is reached
Specifications
- Maximum Roll Width: 100″ (2540 mm)
- Maximum Roll Diameter: 84″ (2134 mm)
- Pneumatic Requirements: 75 PSI (7 kPa)
Specifications can be changed as per customer requirements
How it works
The yarn tension is constantly and accurately measured by the ATC sensor unit, sending a signal to the ATC operator unit.
Inside the operator unit, a motor and gearbox are controlled to automatically adjust the position of the flex-brake on the weft-feeder resulting in consistently stable yarn tension at the level required.