[hfcm id=”28″]
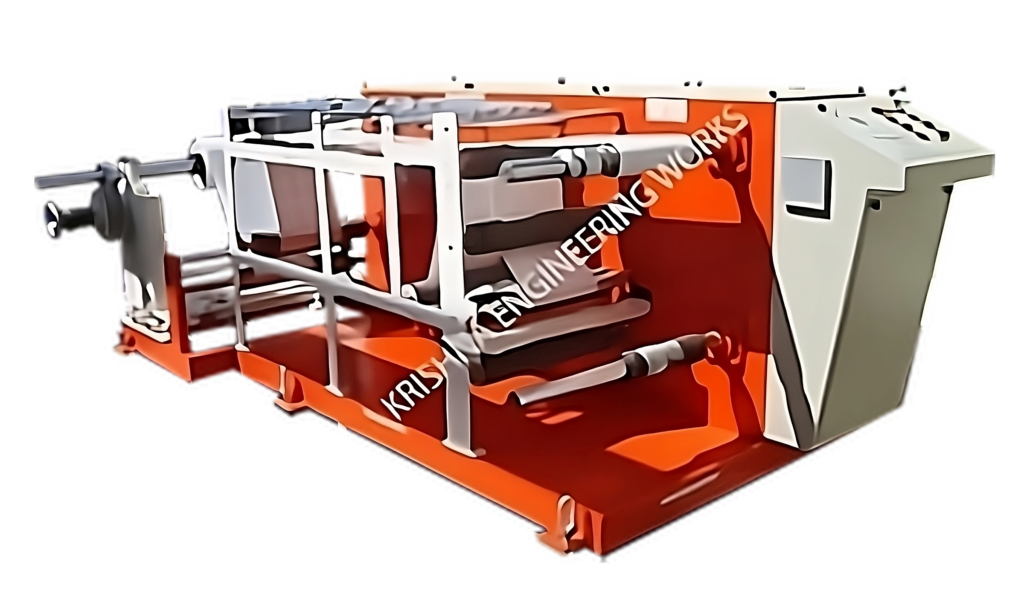
Two Stage Winder – Abhisara International
Two Stage Winder System
System Components:
- Primary Winder Unit
- First stage of winding, designed for initial material accumulation.
- Ensures smooth and controlled initial winding.
- Secondary Winder Unit
- Second stage of winding, completes the winding process.
- Ensures optimal roll formation and consistent tension.
- Tension Controller
- Monitors and adjusts material tension throughout both winding stages.
- Ensures consistent tension for high-quality winding.
- Guide Rollers
- Aligns and guides the material through both winding stages.
- Designed for smooth material handling and precise alignment.
- Proximity Sensors
- Detects the position and movement of the material.
- Provides real-time data for precise tension adjustments.
- Electronic-Pneumatic (E-P) Converter
- Converts electrical signals from the tension controller into pneumatic pressure.
- Adjusts air pressure to control material tension accurately.
- Drive Motors
- Powers the winding units, ensuring consistent and controlled winding speeds.
- Adjustable speed settings for different material types and thicknesses.
Operation Process:
- Material Feeding
- Material is fed into the primary winder unit.
- Guide rollers ensure the material is aligned properly as it enters the system.
- Primary Winding
- Material is initially wound in the primary winder unit.
- Tension controller monitors and adjusts tension to maintain consistency.
- Transfer to Secondary Winder
- Material is transferred to the secondary winder unit for final winding.
- Proximity sensors monitor material position and provide data for tension adjustments.
- Secondary Winding
- Material is wound onto rolls in the secondary winder unit.
- Tension controller ensures consistent tension throughout the process.
Features:
- Dual-Stage Winding: Two-stage process ensures smooth initial winding and optimal final roll formation.
- Proportional Tension Adjustment: Automatically adjusts tension based on material movement and position.
- Real-Time Monitoring: Continuous monitoring of material position for immediate tension adjustments.
- Adjustable Speed Settings: Drive motors with adjustable speeds for different material types and thicknesses.
- High-Precision Guide Rollers: Ensure accurate material alignment and smooth handling.
Benefits of Using the Two Stage Winder System:
- Enhanced Winding Quality: Two-stage process ensures high-quality roll formation with consistent tension.
- Improved Material Handling: Guide rollers and tension controllers ensure smooth and accurate material flow.
- Reduced Downtime: Automatic tension adjustments reduce the need for manual intervention, minimizing interruptions.
- Versatile Application: Suitable for a wide range of materials and winding requirements.
Specifications:
- Maximum Roll Width: 100 inches (2540 mm)
- Winding Speed: Adjustable to meet specific material requirements.
- Pneumatic Requirements: 75 PSI (7 kPa)
- Control Unit Response Time: Fast response for real-time tension adjustments.
- Customizable Specifications: System specifications can be tailored to meet customer-specific needs.
How It Works:
- Tension Measurement: The ATC (Automatic Tension Control) sensor unit continuously measures material tension throughout the winding process.
- Signal Processing: The ATC operator unit receives tension data and adjusts the motor and gearbox accordingly.
- Tension Adjustment: The E-P converter translates electrical signals into pneumatic pressure to adjust tension, ensuring consistent winding.
Abhisara International’s Two Stage Winder System provides efficient and consistent material winding, enhancing product quality and reducing the need for manual intervention in various manufacturing processes.